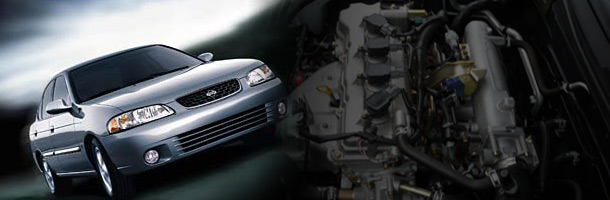
Variable Valves – Plus More
July 12, 2011
By John Thornton. Last time (Fall 2010), we looked at two Nissan variable valve timing case studies, provided by John Thornton. There wasn’t enough room in that issue for John’s very informative third case study, so it’s included here. After we’ve finished with the third case study, we’ll move into an overview of the construction, operation and diagnosis of various crank sensor designs. Let’s get started.
Our third case study involves a 2001 Nissan Sentra GXE, also with the 1.8L QG18DE engine found in the first two case studies.The vehicle failed an Illinois OBD II inspection for a P0335 crank sensor diagnostic trouble code (DTC). If the DTC is cleared, it resets very quickly and matures to a stored DTC. The code definition suggests that a DTC P0335 may be caused by a POS/PHASE sensor synch issue. The engine also surged at idle. Figure 1 illustrates the idle surge in PARK and DRIVE.
The QG18DE engine is equipped with variable intake cam valve timing. By default, the intake cam timing reverts to its fully retarded position. All measurements are in crankshaft degrees.
You’re no doubt familiar with the acronym for top dead center (TDC). If an event occurs before or after top dead center the acronyms BTDC and ATDC are used. Valve events may also occur before or after bottom dead center and the acronyms BBDC and ABDC are used for those.
Without intake cam timing advance (fully retarded):
- the intake valve opens at 3° ATDC
- the intake valve closes at 57° ABDC
- the exhaust valve opens at 38° BBDC
- the exhaust valve closes at 4° ATDC
- valve overlap = 1°
When energized, the intake cam is advanced 20 crank degrees. With intake cam timing advance:
- the intake valve now opens at 17° BTDC
- the intake valve now closes at 37° ABDC
- the exhaust valve now opens at 38° BBDC
- the exhaust valve now closes at 4° ATDC
- valve overlap = 21°
In the 2003 model year, Nissan eliminated the exhaust camshaft sensor on its 1.8L engines. The intake camshaft sensor is used for synch as well as to control intake cam phasing. The intake camshaft sensor is driven off the back of the intake camshaft. The crankshaft reluctor was also changed. It has two missing teeth, followed by 16 teeth, then two missing teeth followed by 16 more teeth. This means there would have been 36 teeth if all were present.
Refer to the waveforms in Figures 2 and 3. The crank (POS) and exhaust cam (PHASE) sensor waveforms are in their usual locations, but we’ve added a third wave format the top. This waveform was produced by the intake camshaft sensor.
When energized, the variable valve timing system should advance the intake cam timing by 20 crankshaft degrees. However, the exhaust cam sensor waveform appears to be retarded by about 10 crank degrees. The timing chain is probably stretched, which also caused the P0355. Although the variable valve timing mechanism causes the intake camshaft to advance as it should, the intake camshaft timing also is about 20 crankshaft degrees retarded. This is probably responsible for the surge. The intake cam sprocket may have jumped a tooth, or there may be another mechanical explanation.
Using an oscilloscope attached to the crank and cam sensors allows us to diagnose engine mechanical faults without engine disassembly. Knowing what you’ll find before you remove a single bolt saves you from a potential misdiagnosis and a lot of wasted time and it also allows you to provide the customer with a more accurate estimate of repair costs.
Crankshaft Position Sensors
The crankshaft position sensor (CKP) helps the PCM determine when each piston reaches top dead center (TDC). To time the ignition event for each cylinder, the PCM calculates the position of the crankshaft’s connecting rod journal in relation to TDC. For example, the PCM might time the spark event to occur at 10° before top dead center (BTDC) on the compression stroke. On 1996 and later OBD II-compliant vehicles, the CKP also detects cylinder misfires by measuring very small variations in crankshaft speed. For example, the crankshaft normally decelerates just as a cylinder approaches TDC on compression stroke.
After combustion, the crankshaft accelerates on the power stroke until about 90° after top dead center (ATDC), when cylinder pressure is expended and the angularity of the connecting rod diminishes. When this very predictable deceleration and acceleration pattern is disrupted on a continuing basis, the PCM stores a misfire trouble code for that cylinder.
Most crankshaft position sensors produce a signal using either variable reluctance (magnetic) or Hall effect sensor. Hall effect sensors produce a digital square wave signal,while magnetic or variable reluctance sensors produce a sine wave pattern. In addition to these basic differences, the amplitude (voltage level) of the output signal of these two sensor types is also different. The Hall effect sensor output voltage level remains consistent throughout the sensor’s operating range. The signal is either off (low) or on (high). In contrast, a variable reluctance sensor’s output will increase in amplitude as engine speed increases. The frequency of the signal produced by both sensors give the PCM a direct indication of crankshaft speed and position.
The magnetic reluctance crankshaft position sensor (Figure 4) consists of a single wire wrapped around a permanent magnet, with each end of the wire representing a positive or negative pole. As a rotating ferrous reluctor tooth passes the sensor, it generates an alternating current (AC) signal to the PCM. The signal varies between positive and negative voltage. The PCM reads the sensor signal as it crosses the zero volt line. The accuracy of the reluctance sensor varies slightly due to the voltage switching from positive to negative at slightly different points along the “zero” line.
The reluctor for the number one cylinder is slightly modified to provide a signature waveform, indicating to the PCM when that cylinder reaches TDC. When diagnosing a magnetic reluctance sensor, it’s important to remember that crank sensor voltage output or amplitude is affected by the air gap between the sensor tip and reluctor, as well as the speed of the reluctor. The accuracy of the reluctance sensor can also be affected if the sensor magnet has attracted particles of ferrous material from clutch linings or other wearing parts.Hall effect sensors are three-wire sensors that produce a square-wave digital signal that is sent to the PCM.
The Hall effect sensor acts as an electrical switch that requires an outside power source and a ground (two of the three sensor wires) to produce the square-wave, on/off output signal (the third sensor wire). Unlike magnetic reluctance sensors, Hall effect crank position sensors don’t rely on higher shaft speeds to generate a useable signal. But like the magnetic reluctance sensor signal, when the crankshaft speed increases, the Hall effect signal frequency also increases.
A somewhat less familiar crankshaft speed sensor is called a magnetoresistive sensor. Similar to magnetic reluctance sensors,magnetoresistive sensors use a permanent magnet, tone wheel and two-wire sensor connection. That is where the similarities end.
First, the magnetoresistive sensor is based on the principle of a magnetic field changing the resistance and the current flow through the sensor itself. The magnetoresistive effect is the change of the resistivity of a current-carrying ferromagnetic material due to a magnetic field.And unlike magnetic reluctance sensors, a magnetoresistive sensor can’t generate a signal voltage on its own, and requires an external power supply from the PCM.
Inside the sensor is a small integrated circuit containing a magnetoresistive bridge. The magnetoresistive bridge changes resistance due to the relationship between the tone wheel and magnetic field surrounding the sensor.
The sensor may contain two magnetoresistive sensors phased slightly apart from each other. Due to this difference in phasing, a magnetoresistive sensor can measure shaft speed and produce a signal at very low rpm.
The sensor’s electronic circuitry modifies and amplifies the varying resistance into a direct current (DC) voltage output signal. As the tone wheel rotates and shifts the magnetic field, the sensor changes the voltage and current levels on the signal circuit to the PCM. The magnetoresistive sensor produces a square-wave signal like a Hall Effect sensor,However, the square-wave signal generally will not pull down to zero volts. Instead, the signal will pull from high to low voltage as the circuit resistance changes.
Other magnetoresistive sensor advantages are:
- Non-contact operation, so there is no wear or friction
- Due to its high sensitivity, it can be used to measure weak magnetic fields
- Wide operating frequency range (0 Hz to 1MHz)
- Low sensitivity to mechanical stress and less sensitive to vibration than inductive sensors
- Can be used in harsh environments and a thigh operating temperatures
We’ll be back next time with some quick CKP test procedures, using a scan tool and other diagnostic equipment.