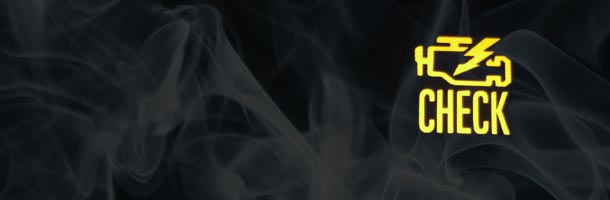
Plug & Play Emissions Testing
August 10, 2010
A number of emissions programs are conducting an emissions test on OBD II vehicles that has been nicknamed a “plug and play” test.
Perhaps something similar to this has already happened to you. A customer brings his vehicle to your shop because the malfunction indicator lamp (MIL) is glowing on the dashboard. After retrieving the stored diagnostic trouble codes (DTCs) and freeze frame data, then conducting a thorough diagnosis, you determine the cause of the fault. The defective part is replaced, the DTCs and freeze frame data are cleared from the Powertrain Control Module (PCM) memory and the vehicle is taken for a road test. After the road test, the PCM’s memory is rechecked for stored or pending DTCs. None are found.
Another successful repair. Time to prepare a bill, collect your money and return the vehicle to the customer.
After a few weeks have passed, you may have nearly forgotten about the vehicle, the original problem or its cause. Then the owner returns, clutching a piece of paper in his hand. He’s just come from the vehicle emissions test center, where they’ve told him that his vehicle has failed its annual emissions test. The MIL isn’t on, the vehicle appears to be running well and no pending DTCs are stored in the PCM’s memory. What gives?
A number of vehicle emissions testing programs across the country are now conducting a new type of emissions test on OBD II-compliant vehicles that has been nicknamed a “plug & play” test. This test does not directly measure the vehicle’s emissions. Instead, the technician at the test center plugs into the OBD II data link connector (DLC) and scans the information available there. If the MIL is on or if any DTCs are stored in the PCM’s memory, the vehicle fails the emissions test right off the bat.
If no DTCs are stored, testing moves to the next level. The technician at the test center uses his test equipment to retrieve information about the vehicle’s OBD II monitors – specifically to see how many are reporting as “Ready.” In many cases, if more than two monitors report as “Not Ready,” the vehicle will be deemed not ready for further testing. Newer vehicles may fail if even one monitor is reporting “Not Ready.” The vehicle owner can’t re-register the vehicle until the reason is found and repaired.
This is the situation that brought the customer back to the shop. The vehicle was running fine, with no stored DTCs, but too many monitors were reporting as “Not Ready.” If the PCM had not stored any DTCs and the required number of monitors were reporting “Ready,” the vehicle would have been ready for the next step. In some areas, the vehicle would then receive a tailpipe emissions test. If it passed, the owner would be allowed to register it for another year. In other cases, a successful DTC and monitor check are all that are required to pass the emissions test.
It’s much quicker and easier to test vehicles using the plug & play method, but how accurate is it? OBD II doesn’t measure emissions directly, but it’s been determined that it is a pretty good judge of a vehicle’s actual emissions output. If it says the vehicle is okay, it should easily pass a conventional or I/M 240 tailpipe emissions test.
Plug & play tests can be conducted much quicker than conventional or I/M 240 tests, which means test centers can process more vehicles per work shift and vehicle owners will spend less time waiting in line. To make things even easier, we may even see the day when each vehicle reports its OBD II status via radio waves as it passes data collection sites along the side of the roadway. This could completely eliminate the need for periodic trips to the emission test center.
OBD II Monitors
Monitors are divided into two basic categories: continuous and non-continuous. As you would expect, continuous monitors run whenever the vehicle is in operation. The comprehensive component monitor is a continuous monitor that keeps tabs on various vehicle sensors and actuators to make sure they are operating properly. The PCM conducts functionality tests on the components under its watch, then compares the results to standards stored in memory. Many of these tests are similar to OBD I tests. They check for components that are shorted or open, or are operating outside the expected range. If a component fails its test, a DTC is stored, just like OBD I.
Another continuous monitor checks for engine misfire. The PCM keeps a careful watch for misfire, due to its potential to cause damage to the catalyst and the increase in vehicle emissions that will result. If misfire is detected, the PCM will turn on the MIL and set a DTC right now; no messing around. When a severe misfire is detected, the MIL will flash, hopefully alerting the driver that a serious malfunction is occurring.
The fuel monitor is the last continuous monitor we’ll discuss here. It watches for excessive fuel corrections caused by an imbalance in the air/fuel ratio. This monitor is designed to immediately detect a problem that might damage the catalyst and therefore increase vehicle emissions. All of these monitors operate on a one trip monitor, so if a problem exists now, the PCM will report it now. No waiting around to see if it will reoccur during a second trip.
Because continuous monitors run all the time and watch for problems as they occur, they are unlikely to be responsible for the kind of emissions test failure described above. If a vehicle has failed a continuous monitor, the MIL will be lit, a DTC and freeze frame data will be stored and the owner will know there is a problem. Taking it to a test center in this condition would result in a guaranteed failure.
Failed plug & play emissions tests are more often caused by problems with non-continuous monitors. Non-continuous monitors include the oxygen sensor monitor, the oxygen sensor heater monitor, the catalyst monitor, the EGR monitor, the EVAP monitor and others.
Unlike continuous monitors, non-continuous monitors only run when certain conditions are met. These conditions are called enabling criteria, and they vary from one monitor to the next and from one vehicle to the next. If the enabling criteria aren’t met, the monitor will not run and the PCM will report “Not Ready” for that monitor. As noted, too many “Not Ready” monitors will result in a plug & play test failure.
The vehicle designers carefully select the enabling criteria so that when a monitor runs, the results will be as accurate as possible and the test will result in as little inconvenience as possible to the vehicle owner. Unfortunately, some monitors may be a little too well designed.
Depending on a driver’s driving habits, it’s entirely possible that some of the vehicle monitors will never run to completion. For example, a senior citizen who rarely drives outside the neighborhood and have a difficult time getting the evap monitor to run to completion. So even though there is absolutely nothing wrong with the vehicle, it would fail a plug & play emissions test because the evap monitor (and possibly others) would report as “Not Ready” at the test center.
It’s your responsibility to make sure that your customer’s vehicles will pass an emissions test after they leave your shop. Each time you clear codes on an OBD II vehicle, you also reset all of the monitors to “Not Ready.” Given enough driving time, most of these monitors will run to completion and report as “Ready” on their own, with no help from you. But the enabling criteria for others may be so specific that they may never run without outside help. This is the reason some test centers will allow a vehicle that has two monitors in the “Not Ready” status to pass the emission test. But the regulations are getting stricter for newer vehicles.
Each monitor has a specific “trip” or drive pattern that allows the vehicle to fulfill the necessary enabling criteria before the monitor runs. A trip may begin as soon as the ignition is turned on, or it may not begin until after engine warm-up or a specified period of highway driving has been met. OBD II regulations have established a “drive cycle” which has been designed to allow all of the trip requirements for the various monitors to be met. Unless the drive cycle instructions are followed in the specified sequence, it’s unlikely that all of the monitors will run to completion.
The following is a summary of generic OBD II drive cycle instructions for a Hyundai:
- The Intake Air Temperature (IAT) should be between 14 and 122 degrees F.
- Barometric pressure should be equal to or greater than 75 kPa.
- The fuel tank should be between 25 and 75% full at the start of the test.
- During acceleration, keep throttle 1⁄4 to 1⁄2 open.
- During deceleration, slow to less than 15 mph at an engine speed of less than 1000 rpm without touching the brake or clutch pedal.
- During cruise, maintain a steady engine speed between 1400 and 4000 rpm.
- At idle speed, keep the throttle closed and the gear selector in the Neutral position.
Remember, these are just the preliminary instructions. The actual drive cycle must conform exactly to the following instructions, or the various monitors may not run to completion.
- The drive cycle begins with a cold engine startup. The IAT must be between 32 and 85 degrees F. Engine Coolant Temperature (ECT)
must be less than 127 degrees F. It may be necessary for the customer to leave the car with you overnight so it can cool down completely. The engine coolant and intake air temperatures must be within a tight range to complete all of the OBD II monitors during the drive cycle. If the IAT input is not between 32 and 86 degrees F at the beginning of the drive cycle, the EVAP monitor will not run. - Start the engine and allow it to idle in Park for one to two minutes.
- Within the first minute and a half, accelerate at 1/4 to 3/4 throttle to 50-55 mph. Hold that speed for 2-3 minutes. Unless your shop is very close to a major expressway, it may be difficult to satisfy this step in the drive cycle.
- Decelerate to 0 mph without braking, then idle for 1-2 minutes. If you’re on an expressway, pull safely off the road during this segment.
- Accelerate to 55 mph, using 1⁄4 to 3⁄4 throttle, then hold a steady cruise for 10 to 20 minutes.
- Return to 0 mph with the engine idling in Park, then turn the ignition off.
All drive cycle testing should be conducted with two people in the vehicle – one to drive and the other to give instructions and monitor any test equipment. Progressive shops located in congested areas and lacking easy access to expressways with light traffic flow have installed chassis dynamometers to conduct drive cycle testing. The dyno allows each step in the drive cycle to be carried out without interruption.
To guarantee a passing score, some shops handle the process from start to finish. After repairs are completed, they run the vehicle through a drive cycle to make sure all of the monitors are set to “Ready.” As a final step, the vehicle is driven to the test center for the emissions test. When the customer picks up the vehicle, a “Pass” certificate is turned over with the invoice.
All of this testing takes extra time, and if the purchase of a dyno is required, lots of extra money. Not only are you diagnosing and repairing the vehicle’s faults, you are also making certain it will pass the emissions test in effect in your area. Make sure the customer understands this value-added service. Many very busy people are perfectly happy to pay to have this chore taken out of their hands. Maintaining good communication with your customers will increase your billable hours.